
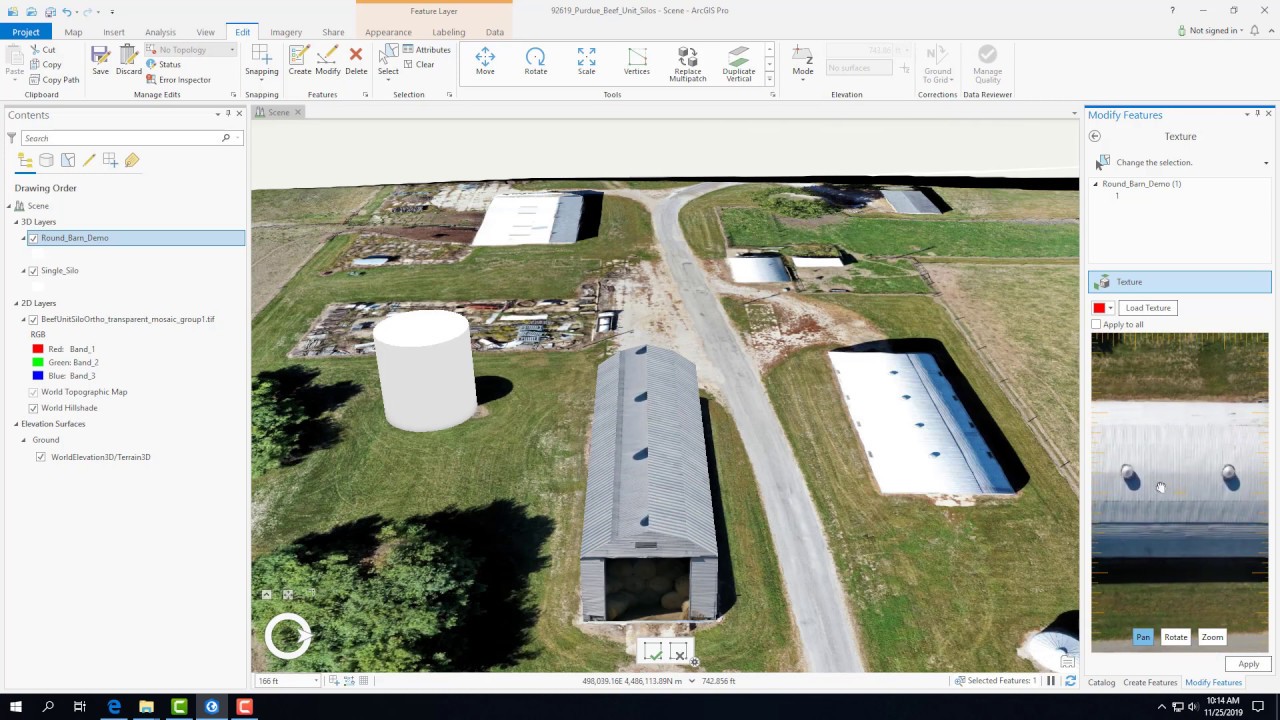
proposed a guideline for an analysis aware design with IGA. In contrast to the application of certain spline technologies, this approach permits the direct usage of common CAD models without any re-discretization and allows seamless back and forth integration into CAD.Ĭohen et al. To allow an immediate simulation upon those descriptions, IGA needs to be enhanced by facilitating trimming and the consideration of multiple patches and their interaction, which results in the isogeometric B-Rep analysis (IBRA). trimming, and joining them to more complex objects. New shapes can be generated by adding different boundary curves to the surfaces, i.e. This approach eliminates the restriction of NURBS being topological rectangles (or cuboids). With this methodology, many possibilities arise for the description of objects. ī-Rep geometrically defines objects by their circumscription, meaning a solid is being described by a set of enclosing surfaces, which themselves have trimming curves, and those have start and end points. However, CAD systems do typically rely on an alternative approach in the shape description, the so-called boundary representation (B-Rep). One avenue to circumvent this restriction has been the introduction of T-Splines, hierarchic splines, and other spline technologies within the scope of IGA, which allowed modeling more sophisticated shapes. However, shaping complex geometries with single entities appears to be demanding, resulting repeatedly in badly conditioned FE models. NURBS maintain a high continuity, which allows a very efficient simulation with typically a moderate number of degrees of freedom. The initial concept of IGA was the use of full, untrimmed NURBS patches, like curves, surfaces and solids. It is a FEM approach directly relying on Non-Uniform Rational B-Splines (NURBS), which is a standard representation within CAD models. have introduced isogeometric analysis (IGA). In opposition to generating FE models by converting the geometry description from CAD, Hughes et al. However, meshing is still time consuming and it does recreate shapes, which corrupts the original bodies and complicates iterative operations. Generating a FE-suitable, meshed geometry can be very complex and error prone, whereby the developments have been enormous to automatize this process. For classical computer aided engineering (CAE) workflows, the drafted geometries would be meshed or extracted into geometrical primitives, such as triangles or quadrilaterals, which are common base forms within FEM. However, it is nowadays employed to fulfill much more tasks, as for example providing a pre- and post-processor for FEM.
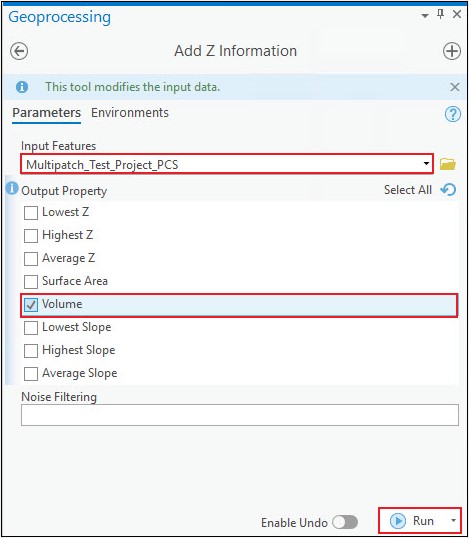

Initially, CAD has been seen as the tool to digitize the drawing board. Ever since the introduction and the subsequent further developments of finite element methods (FEM), computer aided design (CAD)-integrated simulation became a major avenue in the field, as it does provide eased modelling and visualization facilities for complex problems.
